👉 Acesse meu curso: https://www.udemy.com/course/cronoanalise-e/
Por volta de 1900, se você quisesse comprar um carro, teria que visitar um produtor artesanal... sim, um artesão de carros. Provavelmente o dono de uma oficina naquelas quais trabalha toda a família, onde são feitos desde pequenos reparos até a construções de automóveis grosseiros. Após pagar uma fábula, alguns meses depois, certamente você estaria com seu carro "novinho" em folha. Havia uma espécie de satisfação ao se lidar diretamente com o fabricante e a possibilidade de se ter um carro "como você poderia querer", mais ou menos como quando você vai pedir uma pizza, mas quer sem cebola. As principais características eram:
- TRABALHADORES SEMI-INDEPENDENTES, HÁBEIS EM DESENHO, MÁQUINAS E MONTAGEM.
- ORGANIZAÇÕES INDEPENDENTES E DESCENTRALIZADAS, ONDE ELAS MESMAS PRODUZIAM TODAS AS PEÇAS. O DONO TRATAVA DIRETAMENTE COM FORNECEDORES, TRABALHADORES E CLIENTES.
- AS MÁQUINAS TINHAM USO GERAL (FURAR, CORTAR, POLIR, ETC.) - BAIXA PRODUÇÃO COM ALTOS CUSTOS.
A produção artesanal ainda existe, de certa forma e em nichos específicos, como algumas montadoras de carros (Ferrari, por exemplo), fabricantes de relógios e joias. As desvantagens principais da produção artesanal eram:
- SOMENTE ÀQUELES DE ALTO PODER AQUISITIVO TINHAM CONDIÇÃO DE COMPRAR O PRODUTO.
- QUALIDADE DO PRODUTO IMPREVISÍVEL, POIS, TECNICAMENTE CADA PRODUTO ERA UM PROTÓTIPO.
- POUQUÍSSIMAS AÇÕES DE MELHORIAS DE PROCESSO E PRODUTO.
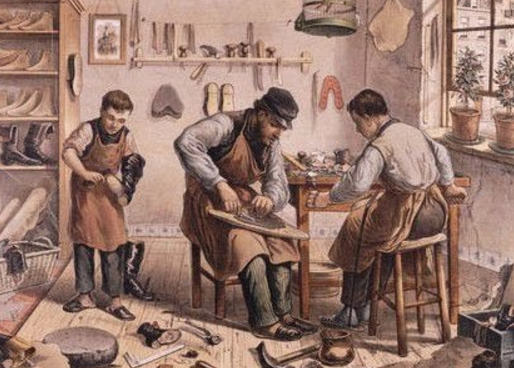
2 – Produção em massa
Um gerente de fundição da Filadélfia chamado Frederick Winslow Taylor deu o start ao que seria um modelo de produção adotado por muitas empresas durante muito tempo, a PRODUÇÃO EM MASSA.
Ele foi o primeiro a aplicar os princípios científicos à gestão e à manufatura. Seu texto "Scientific Management" continua até os dias atuais tratado como clássico pelos entusiastas do assunto e é utilizado como referência em muitas universidades e mesmo em empresas.
Diferente da produção artesanal, onde basicamente o trabalho dependia da habilidade e experiência do artesão, Taylor optou por padronizar a "melhor forma" de se realizar o trabalho, de modo que, teoricamente, qualquer trabalhador pudesse realizá-lo.
O sistema proposto por Taylor deu por separar a produção e o seu planejamento, onde engenheiros industriais, apoiados pelos recentes criados trabalhos de tempos e métodos determinavam a tal "melhor forma" de realizar o trabalho, ou seja, um planeja, outro trabalha conforme foi planejado.

Hoje, o termo "Taylorismo" é, de certa forma, mau ouvido e mau visto por muitas pessoas, pois traz consigo um estereótipo de trabalho desumanizado e engessado, no entanto, apesar de a produção em massa ter se desenvolvido nas raízes do Taylorismo, não foi essa a ideia proposta por Taylor e mesmo conceitos atuais de produção (como a produção enxuta) devem muito ao trabalho de Taylor. As principais contribuições de Taylor que se enraizaram em qualquer sistema de produção (puxado ou empurrado, qualquer) são:
- Trabalho Padronizado (como instruções de trabalho);
- Tempo de ciclo reduzido;
- Estudos de Tempos e Métodos.

Buscar formas de gerenciamento que aumentem, principalmente, a produtividade, é um desafio presente na rotina dos gestores (e outros) desde muito tempo com a Revolução Industrial e sua força impulsionadora do século XIX, as organizações encararam uma nova realidade, e o crescimento das indústrias exigiu o desenvolvimento de métodos capazes de gerir os processos, de modo que a produtividade fosse alta, garantindo a competitividade dos produtos. Taylor observou práticas ruins na administração e nas atividades fabris, tais como:
• Falta de divisão de responsabilidades dos administradores;
• Falta de incentivos para melhorar o desempenho;
• Falta de integração entre departamentos;
• Trabalhadores executando tarefas para as quais não possuíam aptidão;
• Conflitos entre funcionários da produção x administração sobre a quantidade a ser produzida, etc.
Um dos primeiros problemas que o Taylorismo atacou foi o problema da remuneração dos funcionários da produção, para isso, estudou o tempo e definiu o tempo-padrão, da seguinte forma: Quanto tempo um trabalhador precisa – dando o melhor de si – para fazer seu trabalho? Para conseguir definir isso, Taylor dividiu cada tarefa em “microprocessos”, e utilizando os próprios trabalhadores, cronometrou e registrou o tempo necessário para cada tarefa. A partir disso, tornou-se possível calcular os salários de acordo com a quantidade produzida (o que já era feito antes), porém, agora baseado em um estudo de tempo. Com isso, o trabalhador fabril também ganhou uma motivação para produzir da melhor forma com o máximo de empenho, a fim de garantir um salário razoável.
Vale citar que o aumento da produtividade proposto por Taylor não exige um esforço físico maior do funcionário, mas sim de uma eficiência no processo, ou seja, trabalhar de forma inteligente, por isso há o estudo de tempos e movimentos, que busca melhorar em eficiência o trabalho nas fábricas.
Taylor revolucionou a administração das fábricas e isso gerou melhorias. Os anos passaram e as ideias propostas por Taylor (e outros nomes que também trabalharam no desenvolvimento de uma nova administração, como os Gilbreth, Henry Gantt – sim, aquele que propôs um método gráfico para acompanhar a produção, e que hoje é utilizado até em planos de negócio – e outros nomes), continuam mais atuais do que nunca, afinal, como nos diz Antonio Maximiano: nada mais atual do que o combate ao desperdício e o aumento da eficiência.
Sabendo disso, inúmeras empresas viam nas propostas de Taylor a solução para manterem-se produtivas e competitivas (isso significa, principalmente, um baixo custo produtivo que será alcançado utilizando métodos de produção eficientes). A eficiência é a palavra mestra do trabalho, por isso diversas empresas buscam profissionais especializados para avaliarem seus processos e proporem melhorias, alcançando, assim, diminuição dos custos e maior eficiência.
3 – A proposta de Ford
Henry Ford (1863-1947) dedicou o principal esforço de sua vida – segundo a opinião de muitos estudiosos da administração – ao desenho de um automóvel de fácil fabricação, manutenção e troca de componentes e isso tornou possível a linha de montagem automotiva.
Objetivando a fácil intercambiabilidade , Henry Ford padronizou o uso de peças em cada operação. Ford desenhou um motor mais simples, com reduzido número de peças móveis, por exemplo, o bloco de motor era feito de uma peça única fundida ao passo que os concorrentes fundiam cada válvula individualmente, unindo o motor por parafusamento. Isso reduziu um grande custo com ajuste de peças. Somando-se o fato de que o reparo fácil por parte do usuário foi atingido, elevou-se o nome da Ford ainda mais frente aos concorrentes.

Havia, no entanto, um enorme problema. A coordenação de um sistema de produção baseado na linha era bastante problemática, visto que pessoas diferentes trabalham com ritmos diferentes e isso gera uma instabilidade no sistema, o que gerava transtornos, tais quais a imprevisibilidade da produção, além de produtividade e eficiência baixas.
Observando tal fato, Henry Ford iniciou a entrega das peças aos colaboradores da linha, com o objetivo de reduzir seu tempo de caminhada até o estoque para busca-las, deixando o colaborador focado somente em produzir. Melhores resultados foram conseguidos com essa melhoria no sistema. Baseando-se ainda nas propostas de tempos e métodos de Taylor, Ford teve o insight da linha de produção em movimento, sistema no qual o automóvel se move ao longo da linha, o automóvel vai até o operário para que este lhe faça a operação, tornando conectados – de fato – processos sequenciais, além de um macro balanceamento dos tempos, uma vez que agora, como a linha se move em velocidade fixada, colaboradores mais lentos precisaram acelerar suas atividades e colaboradores mais rápidos, reduziram a velocidade.

A linha de montagem em movimento, somada à redução das atividades necessárias de cada colaborador e o projeto mais simples do automóvel levaram a Ford à liderança mundial no segmento.
Houveram - como consequência - pontos negativos, como em qualquer sistema, tais quais uma grande alienação dos trabalhadores, movimentos sindicais constantes para redução de jornadas de trabalho, além de quê, a qualidade acabava por ficar em segundo plano. Maquinários cada vez maiores, focados em produzir um único componente, grandes estoques e uma produção não baseada, primordialmente, na demanda resultavam em um custo bastante alto para os processos.
4 – O nascimento do TPS
Kiichiro Toyoda, presidente da Toyota Motor Company, se viu diante de um grande dilema para a época – a demissão de 25% do quadro de funcionários devido à crise econômica da empresa. Agravava-se o fato, principalmente devido às políticas sindicais americanas já terem grande influência sobre os sindicatos japoneses. Após uma extensa negociação com o sindicato, foi decidido que:
- 25% do quadro de funcionários seria, efetivamente, demitido;
- Kiichiro Toyoda renunciaria ao cargo;
- Os funcionários não demitidos da Toyota receberam garantias – emprego vitalício e pagamento atrelado à senioridade e lucratividade da empresa, além de moradia e recreação.
Em contrapartida, os funcionários deveriam ser flexíveis quanto às suas funções e terem interesse direto na melhoria dos resultados da empresa, uma vez que estes também se beneficiariam. Assim, nasce um vínculo trabalhador-empresa jamais visto até então.
Uma vez que, agora os funcionários eram custo fixo da empresa, fazia todo o sentido investir nestes e melhorá-los, para que dessa forma pudessem extrair o máximo de capital humano destes.
Esse constituiu um dos fatores-chaves do sucesso do novo modo de produção que surgiria.
Taiichi Ohno, entendendo que os trabalhadores eram o bem mais precioso da organização, sabia que a retenção de informações por parte destes, informações quais poderiam melhorar os processos não deveriam ser perdidas (ou que morressem com estes). Taiichi Ohno e sua equipe envolveram os trabalhadores em atividades de melhoria dos processos, com participação efetiva, o que até então era algo inovador.
Como qualquer gestor de produção, Taiichi Ohno enfrentou grandes problemas, mas superou cada um deles, tal como a baixa quantidade de capital disponível não permitiria que uma prensa fizesse somente um modelo de peça, mas cada máquina da Toyota precisaria estampar uma determinada família de componentes, logicamente, numa quantidade menor do que as aplicadas no complexo Rouge e envolvendo as melhores práticas para troca de ferramentas, sem perda excessiva de tempo.

Os capítulos seguintes tratarão das ferramentas implantadas por Taiichi Ohno e a equipe Toyota, ferramentas quais foram – e são – testadas durante muitos anos e levaram a Toyota a um patamar de excelência e liderança.
............................................................................................................................
Ao perguntarem a Ritsuo Shingo, filho de Shigeo Shingo (um dos nomes que serão abordados nos capítulos a seguir) sobre como ele descreveria o TPS nos dias atuais, uma equipe obteve a seguinte resposta:
“TPS é o acúmulo de pequenas ideias de todo mundo.
(...) Mesmo o TPS, está mudando. O TPS no passado não é o TPS de agora. Mudando, dependendo da situação. O TPS é muito flexível e tentamos ajustá-lo a uma situação atual.
Você não precisa ser muito rígido. Oh! Esse é o TPS? Vou copiar isso. NÃO! Você conhece o TPS, digere o TPS então aplica a uma situação.”
Ver: https://www.youtube.com/watch?v=RZPcXo72Sas
.............................................................................................................................
O TPS foi desenvolvido para salvar a Toyota da falência e levá-la à excelência, mas não é um modelo aplicável somente em indústrias automotivas ou de autopeças. Como cita Ritsuo Shingo, é um sistema flexível. Podemos aplicá-lo, todo ou em parte, na maioria dos segmentos industriais.
Para efeito, quando nos referirmos a TPS, Lean Manufacturing ou Produção Enxuta, estaremos nos referindo ao mesmo sistema.
“TPS significa produzir mais com menos – princípio da eficiência”